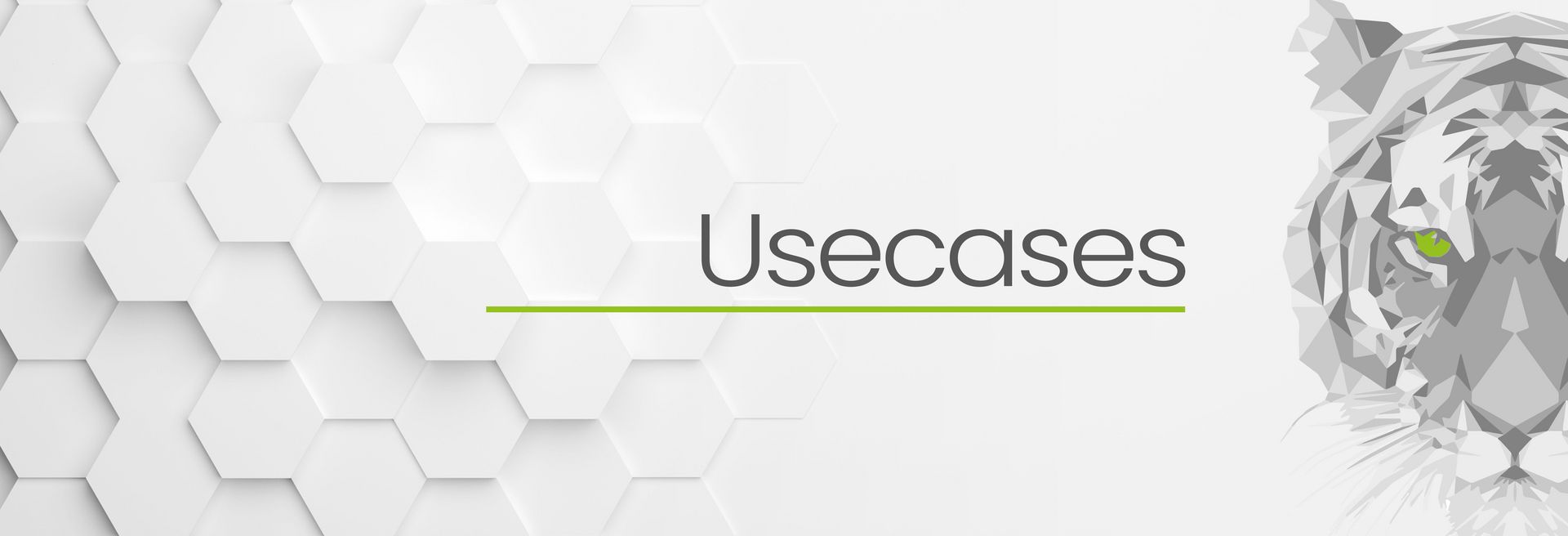
Project description
Industry/application group:
Interior components for commercial vehicles and buses
Result:
3D print of flame-resistant duroplastic components according to UN ECE 118-03 and UL 94-V2 for effective spare parts management of interior components for commercial vehicles and buses.
Spare parts storage as a challenge
Buses are designed for a long service life and are often in use for decades. However, the corresponding supply of spare parts and their long-term storage poses challenges such as warehousing and cost efficiency. Long-term storage can also lead to quality losses and losses in performance, which results in an increased need for spare parts.
Conventional supply of spare parts via injection molding is cost-intensive and can affect the supply chain since the tools often have to be reactivated, partially revised, parameterized and tested in a suitable injection molding machine.
Additive manufacturing presents a cost-effective, needs-based alternative.
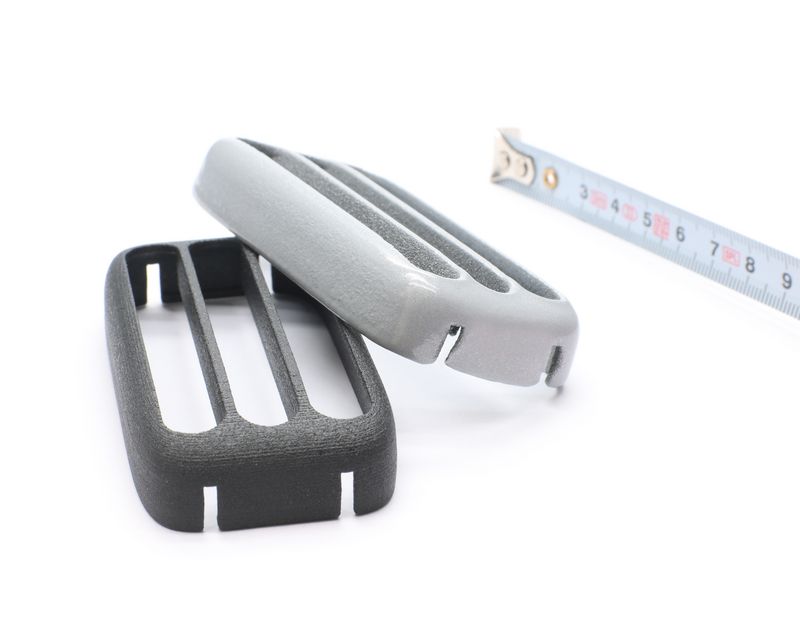
Flame-retardant spare parts from the 3D printer
Components for mass transportation such as buses require special flame resistance properties. Thermoplastics are often not able to meet these requirements in terms of drip resistance - especially with regard to the regulations of UN ECE R118 bus fire standard, Annexes 6, 7 and 8.
The variety of individually configurable components for commercial vehicles and the resulting high complexity of their maintenance place additional demands on the service partner.
Innovative 3D printing processes close this gap and offer numerous other advantages for OEMs and vehicle owners:
- Reduced carbon footprint
- Extended service life of commercial vehicles
- Sustainability through a prolonged product life cycle
- Highly efficient fast, customizable component procurement
- Effective cost-benefit factor through quick adjustment of spare parts
- Smaller production quantities
- Lower storage costs
- Consistently high product quality
Checked and tested:
TIGITAL® 3D-Set print material
PPP 371/80002
With completely new duroplastic-based materials for SLS 3D printing, TIGITAL® 3D-Set has developed an innovative material class that has been specially tailored to the quality requirements of bus manufacturers.
TIGITAL® 3D-Set PPP 371/80002 fully complies with the UN ECE R118-03 standards and has passed emissions testing for vehicle interiors according to VDA.
Approval and Additive Manufacturing
After the final component approval, the OEM has several options for the additively manufactured spare part:
- An approved spare parts partner prints the desired object according to OEM specifications
- The OEM commissions a 3D printing service partner for additive manufacturing
- The OEM manufactures its own spare parts with its own SLS 3D printer
Coated, printed and delivered
3D printed components can be powder coated with TIGER Drylac® and printed with TIGITAL® Inks. This allows both the optical properties and the service life of an object to be improved in a targeted manner.
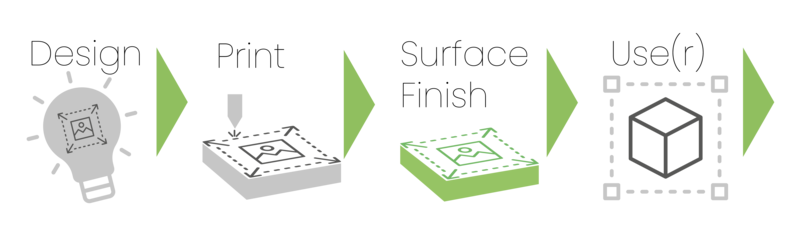
"TIGITAL® 3D-Set PPP 371/80002 represents an innovation in the field of flame-retardant materials based on duroplastics. We are enthusiastic about the properties of the product - both in terms of printability and in terms of the component properties that can be achieved with it. Tests on Farsoon 252P series have been overwhelmingly successful and we will continue to intensify cooperation with TIGITAL® 3D-Set.”
Dirk Simon | Chief Executive Officer, Europe | Farsoon
INFORMATION TO THE USER - DISCLAIMER
TIGER’s verbal and written recommendations for the processing, use and application of our products, including the information, product properties (e.g. mechanical properties and emission properties) and processing parameters (e.g. laser power, part bed temperatures, post-curing conditions) provided in this use case, are based upon our experience and in accordance with present technological standards. These are given only in order to support the user, are noncommittal and do not constitute any additional commitment or product specification. The user shall be solely responsible for checking and verifying the suitability and/or fitness of our products and exemplary processing conditions for the intended use, application and process. Further, the user shall be solely responsible for the appropriate, safe and legally compliant use, processing, handling and application of our products as well as for any related 3D printed parts. To the extent permitted by applicable law, TIGER, its employees, boards, OWNERS, agents, subcontractors or affiliates can NOT be made liable for any damages, whether caused directly or indirectly BY or being related to this use case, or for any related loss of profit, loss of goodwill, or any other consequential damages.
Back to overview