TIGITAL® 3D-Print - Frequently asked questions
Welcome to our FAQ page! As a young and innovative business, we understand that you may have a lot of questions about our products and services. That's why we've put together this page to address some of the most common inquiries we receive from our customers.
Whether you're an experienced 3D printing professional or just getting started in the industry, we're confident that you'll find the answers you need here. Our team of experts has put together a comprehensive collection of information on everything from the materials we use to our production processes and beyond.
If you're looking to learn more about our Materials and how they can benefit your business, you've come to the right place. Take a look around and don't hesitate to contact us if you have any further questions or concerns.
TIGITAL® 3D-Set is a thermoset material. A type of polymer that undergoes a chemical reaction during curing, which irreversibly transforms it into a hardened, infusible, and insoluble state. Unlike thermoplastics, which can be melted and re-molded multiple times, thermosets cannot be reprocessed once they have been cured.
The curing process of thermoset materials involves a crosslinking reaction, where the polymer chains form a three-dimensional network structure. This crosslinking is typically triggered by heat, chemical catalysts, or radiation. Once cured, the material retains its shape and mechanical properties even at high temperatures, making it suitable for applications requiring dimensional stability and resistance to heat, chemicals, and electrical conductivity.
Common examples of thermoset materials include epoxy resins, phenolic resins, polyurethanes, and unsaturated polyester resins. These materials find widespread use in various industries, such as aerospace, automotive, electrical insulation, coatings, adhesives, and composite materials.
Thermoplastics and thermosets are two distinct categories of polymers with significant differences in their behavior, processing, and properties. Here are the key differences between thermoplastics and thermosets:
- Molecular Structure: Thermoplastics are linear or branched polymers composed of long, flexible polymer chains held together by weak intermolecular forces. This allows the chains to slide past each other when heated, leading to their characteristic melt and re-moldability. In contrast, thermosets have a crosslinked or networked molecular structure. The polymer chains are chemically bonded together through covalent crosslinks, resulting in a rigid, three-dimensional network. This crosslinked structure makes thermosets infusible and irreversible.
- Behavior under Heat: Thermoplastics soften when heated and can be molded or reshaped repeatedly. They solidify upon cooling without any significant change in their chemical structure. In contrast, thermosets undergo a curing process during which they irreversibly harden. Once cured, they do not melt or soften upon heating but instead tend to decompose. The crosslinks in thermosets prevent them from being remolded or reprocessed.
- Processing Methods: Thermoplastics can be processed using a variety of methods such as injection molding, extrusion, blow molding, and thermoforming. These methods take advantage of the material's ability to melt and flow. Thermosets, on the other hand, are typically processed in a liquid or soft state before curing. Common processing techniques for thermosets include compression molding, transfer molding, and resin infusion.
- Mechanical Properties: Thermoplastics exhibit toughness, ductility, and good impact resistance. They can deform under stress and return to their original shape upon the removal of the stress. Thermosets, due to their crosslinked structure, possess high strength, stiffness, and dimensional stability. They are generally more rigid and brittle compared to thermoplastics.
- Recycling and Environmental Impact: Thermoplastics can be melted and reprocessed multiple times, making them more recyclable than thermosets. This reusability contributes to their reduced environmental impact. In contrast, thermosets, once cured, cannot be easily recycled or reprocessed. However, some advancements in thermoset recycling technologies are being developed to address this limitation.
It's important to note that within each category, there are numerous types of thermoplastics and thermosets, each with its own specific properties and applications. The choice between thermoplastics and thermosets depends on the desired characteristics and requirements of a particular application.
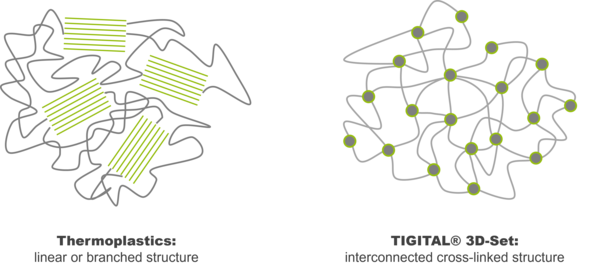
There are numerous types of thermoplastic materials available, each with its own unique properties and applications. Here are some common examples of thermoplastics:
- Polyethylene (PE): Polyethylene is a widely used thermoplastic known for its excellent chemical resistance, low cost, and good impact strength. It is commonly used in packaging films, bottles, pipes, and various molded parts.
- Polypropylene (PP): Polypropylene is a versatile thermoplastic with a high strength-to-weight ratio, good chemical resistance, and high melting point. It finds applications in packaging, automotive parts, textiles, household goods, and medical devices.
- Polyvinyl Chloride (PVC): PVC is a thermoplastic known for its durability, chemical resistance, and flame retardancy. It is used in a wide range of applications such as pipes, electrical cables, flooring, and vinyl siding.
- Polystyrene (PS): Polystyrene is a lightweight and rigid thermoplastic commonly used in packaging, disposable utensils, insulation, and consumer goods.
- Polyethylene Terephthalate (PET): PET is a thermoplastic with excellent clarity, barrier properties, and recyclability. It is widely used in beverage bottles, food packaging, fibers, and films.
- Acrylonitrile Butadiene Styrene (ABS): ABS is a tough and impact-resistant thermoplastic with good dimensional stability. It is commonly used in automotive parts, electronics, toys, and appliances.
- Polycarbonate (PC): Polycarbonate is a transparent thermoplastic with high impact strength, excellent optical clarity, and heat resistance. It is used in applications such as safety glasses, automotive parts, electrical enclosures, and consumer electronics.
- Polyamide (Nylon): Nylon is a strong and lightweight thermoplastic known for its excellent mechanical properties, chemical resistance, and wear resistance. It is used in applications such as automotive components, gears, bearings, and textiles.
- Polyetheretherketone (PEEK): PEEK is a high-cost material high-performance thermoplastic compared to other thermoplastics. It is known for its excellent mechanical properties, chemical resistance, high temperature resistance, and dimensional stability. PEEK is utilized in various industries such as aerospace, automotive, electrical engineering, oil and gas, medical, and chemical processing. It is commonly employed in applications including aerospace components, bearings, seals, pumps, electrical connectors, and structural parts.
- Polyetherimide (PEI): Ultem is another high-performance thermoplastic. It is known for its excellent thermal and mechanical properties, high strength, and dimensional stability. PEI is commonly used in applications that require durability, resistance to high temperatures, and good electrical properties. PEI is used in various industries and applications, including aerospace, automotive, electrical and electronic components, medical devices, and consumer goods. Common uses of PEI include aircraft interiors, automotive components, electrical connectors and insulators, circuit boards, and medical equipment.
These are just a few examples of thermoplastic materials, and there are many more available with different characteristics and applications. The choice of thermoplastic depends on factors such as the required mechanical properties, chemical resistance, heat resistance, and cost for a particular application.
PLA | PVB | PETG | ASA | ABS | PC | PA | PP | |
Water | A | A | A | A | B | A | A | A |
IPA 75% | C | D | A | B | B | B | A | A |
IPA 99% | C | D | B | B | B | B | A | A |
Acetic acid 8% | B | C | A | A | B | A | C | A |
Sodium chloride 10% | B | B | A | B | A | A | A | A |
Citric acid | B | B | A | A | - | A | B | A |
Hydrochloric acid 37% | C | - | A | C | C | A | D | A |
Hydrogen peroxide 30% | B | - | A | A | A | A | D | A |
Phosphoric acid 96% | C | - | C | - | A | A | D | A |
Nitric acid 69% | D | - | D | - | - | D | D | A |
Sulphuric acid 96% | D | - | D | - | - | D | D | A |
Fridex | B | B | A | A | - | A | - | - |
Savo | B | B | A | A | - | B | A | A |
Ethanol | C | D | B | B | A | B | A | A |
Acetone | D | D | C | D | D | C | A | A |
Another very popular hence expensive material for 3D-printing is PEEK. PEEK is a high performance polymer with very high mechanical properties and very high thermal and chemical resistance. These properties make it very difficult to handle and print this kind of material with a very poor reuse factor. Next to this in most of the cases the material is too expensive to be 5/20 used on a broader scale.
The most common 3D printing processes, also known as additive manufacturing processes, can be categorized into several main types:
- Fused Deposition Modeling (FDM) or Fused Filament Fabrication (FFF):
FDM/FFF is one of the most widely used 3D printing processes. It involves melting and extruding a thermoplastic filament through a heated nozzle, which deposits the material layer by layer to create the object. The filament is typically made of materials like ABS, PLA, or PETG. FDM/FFF is known for its affordability, ease of use, and versatility.
- Stereolithography (SLA):
SLA uses a liquid resin that is cured or solidified using a light source, typically a laser or UV light, to create the desired object layer by layer. The liquid resin is photosensitive and solidifies when exposed to the light source. SLA is known for its ability to produce highly detailed and accurate prints with smooth surface finishes. It is commonly used in applications that require high precision and quality, such as prototyping and jewelry making.
- Selective Laser Sintering (SLS):
SLS involves the use of a high-powered laser to selectively fuse powdered materials, typically polymers or metals, layer by layer. The laser heats and melts the powdered material, allowing it to solidify and form the desired shape. SLS can produce complex geometries and functional parts with good mechanical properties. It is often used for prototyping, low-volume production, and in industries like automotive and aerospace.
- Digital Light Processing (DLP):
DLP is similar to SLA but uses a digital light projector instead of a laser to cure the liquid resin. The projector displays the entire layer of the object at once, solidifying the resin where the light is projected. DLP offers faster print speeds compared to SLA but may have slightly lower resolution. It is commonly used in applications where speed is a priority, such as dental and jewelry industries.
- Selective Laser Melting (SLM) and Direct Metal Laser Sintering (DMLS):
SLM and DMLS are 3D printing processes used for metal parts. These processes involve using a high-powered laser to selectively melt and fuse metal powder particles, layer by layer, to build up the desired object. SLM and DMLS are capable of producing complex, fully dense metal parts with excellent mechanical properties. They are commonly used in industries such as aerospace, automotive, and medical.
These are some of the most common 3D printing processes, each with its own advantages, materials, and applications. It's worth noting that there are other 3D printing processes as well, such as Binder Jetting, Electron Beam Melting (EBM), and Laminated Object Manufacturing (LOM), which are used for specific applications and materials.
The material is used in Selective Laser Sintering (SLS) and can be processed at a very low printing temperature and a very low laser energy at the same time which makes it an excellent choice for energy efficient production.
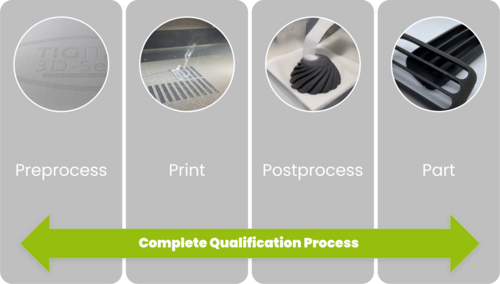
All industries running on SLS are open to use TIGITAL 3D-Set. The focus is on industries wanting to overcome the typical weaknesses of thermoplastic materials and to take advantages of TIGITAL 3D-Set, which are:
- higher flame retardancy
- higher mechanical properties under heat
- no dripping behavior under heat and > higher dimensional stability under heat (no melting)
- high electrical insolation
- higher dimensional stability under heat (no melting)
- high chemical resistance.
These companies are however not limited to in the following industries:
- rail industry
- mass transportation as buses
- E&E (Electronical and Electronics)
- aerospace
- defense
TIGITAL 3D-Set is a thermoset material used for Additive Manufacturing (3D-printing) processes. The chemical back bone for those materials are epoxi and polyester based.
Most popular chemistries are polyester, epoxi, polyurethane, acrylic chemistries
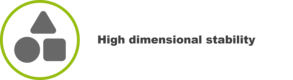
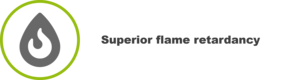
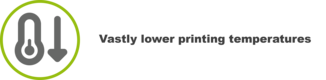
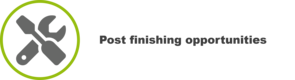
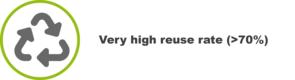
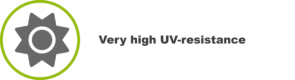
TIGITAL 3D-Set has a wide array of applications but is normally used when high heat resistance and flame retardancy in combination with resistance to chemicals is required. This can be electrical boxes for hydraulics or in mass transportation, but also for applications with the need to withstand outdoor UV-exposure.
In general, thermoset materials may be resistant to weak acids, alkaline solutions, alcohols, esters, ketones, ethers, hydrocarbons, chlorinated hydrocarbons, benzene, motor oils, brake fluids, gasoline, mineral oils, animal and vegetable oils and fats. Additionally, some recent testing from a material supplier has indicated thermosets have good resistance against xylene, glycerin and salt water.
Thermosets are widely used in automotive transmission components that are continuously exposed to harsh chemicals such as oils, gas, transmission, brake and cooling fluids. Whereas thermoplastics such as Nylon will degrade over time when exposed to certain chemicals, thermoset components remain dimensionally and chemically stable over a certain lifetime of a component.
The Heat Distortion Temperature (HDT) is a measure of a material's ability to withstand elevated temperatures without undergoing significant deformation. It is a critical property for thermoplastic materials, particularly those used in applications where exposure to heat is expected, such as in automotive components, electronic devices, or industrial equipment.
The HDT is determined by subjecting a test specimen to a defined load while gradually increasing the temperature. The temperature at which the specimen deforms or deflects a specific amount (typically 0.25 mm or 0.010 inches) is considered the Heat Distortion Temperature. The HDT is usually reported in degrees Celsius (°C) or degrees Fahrenheit (°F). The specific measurements are carried out according to ASTM D648 and ISO75.
The HDT is an essential parameter for material selection and design, as it indicates the temperature range within which a thermoplastic material can maintain its structural integrity without undergoing excessive deformation or failure. Different materials have different HDT values, and it is important to choose a material with a suitable HDT for the intended application to ensure long-term performance and reliability.
Specifically for TIGITAL® 3D-Set the HDT value is approximately between 60°C and 110°C depending on other properties as flexural modulus and impact strength of different materials.
Our PPP series thermosets are flame resistant according to a wide variety of standards. The term flame resistance refers to the ability of materials to resist ignition, flame spread, and the propagation of fire. Different plastics exhibit varying levels of flame resistance, depending on their chemical composition and additives.
Several factors contribute to the flame resistance:
- Ignition Resistance:
Some plastics have inherent resistance to ignition, meaning they are difficult to ignite. For example, polypropylene (PP) and polyethylene (PE) have relatively high ignition resistance compared to other thermoplastics.
- Flame Retardant Additives:
Flame retardant additives can be incorporated into plastics to enhance their flame resistance. These additives work by interrupting the combustion process, reducing the release of flammable gases, or forming a protective char layer on the material's surface. Common flame retardant additives include halogenated compounds, phosphorus-based compounds, and mineral fillers.
- Material Thickness: Thicker plastic parts generally have better flame resistance than thin sections. A thicker material takes longer to heat up and can help prevent the spread of flames.
- Oxygen Index: The oxygen index is a measure of a material's ability to support combustion in the presence of oxygen. It represents the minimum concentration of oxygen required to sustain flaming combustion. Plastics with higher oxygen index values are generally more flame-resistant.
- Testing Standards: Flame resistance is often evaluated through standardized tests such as UL 94 (Underwriters Laboratories) and ISO 1210. These tests assess parameters such as ignition resistance, flame spread, and the self-extinguishing behavior of thermoplastics.
It is important to note that even flame-resistant plastics have limitations and may burn under certain conditions. It is crucial to consider specific regulations, standards, and the application requirements when selecting a material for flame-resistant applications.
A variety of standards can be fulfilled with TIGITAL® 3D-Set:
Norm | Industry | Related Norm |
DIN 54341 | Rail transportation, seatings | DIN 5510-2 (Seating systems) |
DIN 75200 | Passenger cars Interior | FMVSS 302, burning speed, JIS D1201, ISO3795 |
PV3357 | VW Norm | - |
DIN 45545-2 | Flame retardancy in rail transportation | - |
ECE-R118 | Flame retardancy for Interior of mass transportation cars as buses, Annex 6,7,8 |
|
FMVSS 302 | US Federal motor Vehicle Safety Standard | IEC 60695, ISO3795, DIN 75200, JIS D1201 |
UL 94 | Flammability of Plastics 5-VA, HB, V-0/1/2 | Partly ISO10351, partly IEC60695-11-10 |
The shrinkage of the parts is under 2% depending on the part geometry and needs to be determined specifically for any part to adjust printing parameters and other corrective measurement factors.
(PPP materials, TPP materials, HPP materials)
Characteristics | Methods | Units | Serie PPP 371 | Serie TPP 371 | Serie HPP 370 |
Tensile Modulus | ISO 527 | [MPa] | 2100-3200 | 3300 | 3300 |
Tensile Strenght | ISO 527 | [MPa] | 40 | 45 | 50 |
Elongation at Break | ISO 527 | [%] | 2 - 5,5% | 2,4 - 6% | 3 |
HDT-A, 1.8mPa | ISO 75 | °C | 65/80 | Up to 100 | 65 |
Flame retard. ECE R118 | Annex 6 | 2,5 & 3 mm | OK | NA | NA |
Flame retard. ECE R118 | Annex 7 | 2,5 & 3 mm | OK | NA | NA |
Flame retard. ECE R118 | Annex 8 | 3 mm | OK | NA | NA |
UL94 V0 | 3,5 mm | OK | NA | NA | |
UV-Resistance | ++ | +++ | + | ||
Chemical Resistance | +++ | +++ | +++ |
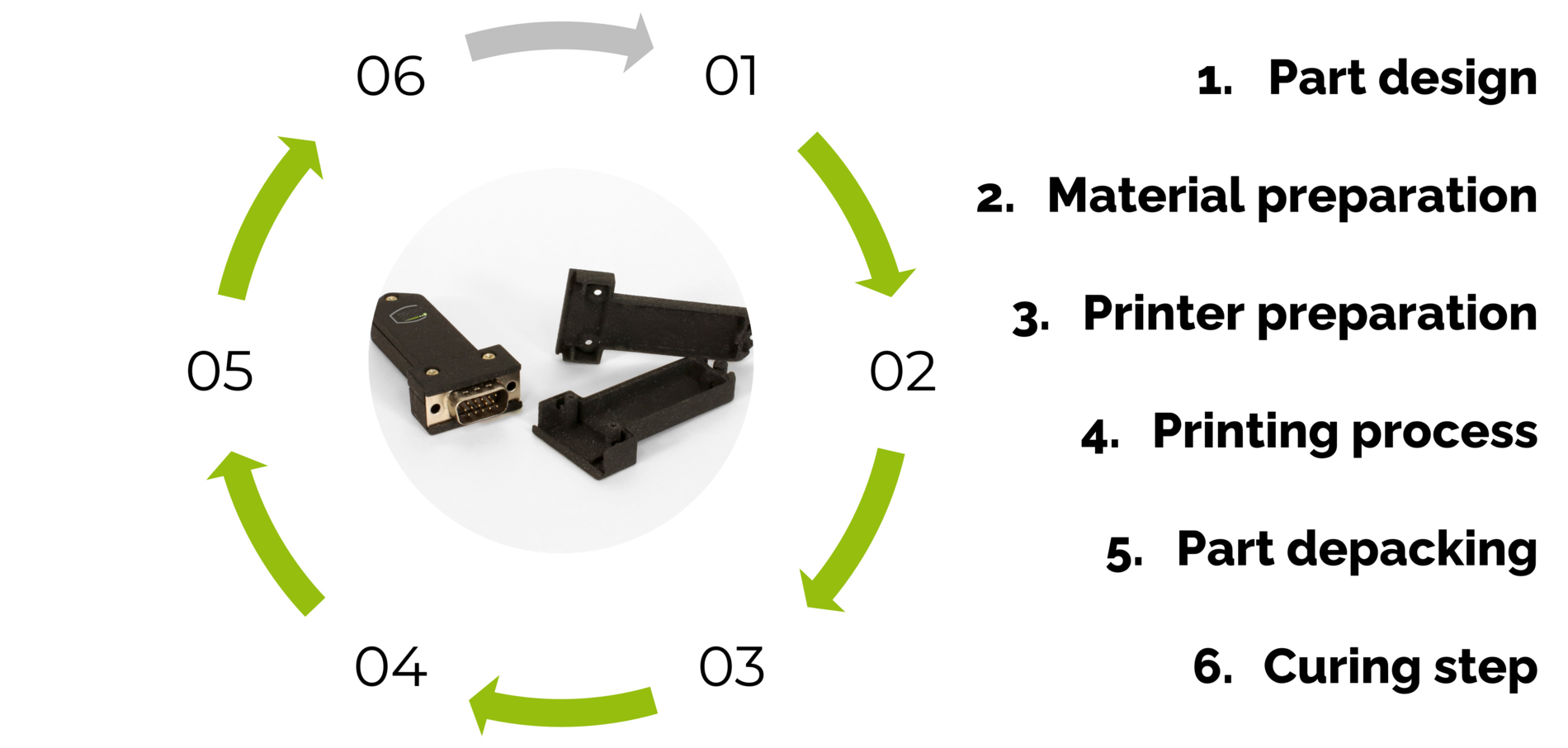
Our materials can be used basically on all open SLS-printers which means that parameter settings are adjustable. There are more and more available machines on the market where we tested our materials on:
- Farsoon
- Prodways
- Weirather
- Sinterit
- EOS printer
- XYZ (now Nexa 3D)
The most important printing parameters to adjust are:
- Build temperature
- Laser energy
- Laser hatch distance
Basic settings Farsoon printer
Temperatures | Z (mm) | Warm Up | Build | Cool down |
Part Temperature [°C] | 0 | 40 | 67,5 | 67 |
1,5 | - | 67,5 | 50 | |
2 | 67,5 | 67,5 | Off |
Laser parameter | Build |
Fill Laser Power [W] | 31 |
Fill Distance [mm] | 0,13 |
If you need more information, we are able to provide specific parameter settings for different machines and materials. Our lab team has carried out settings for all open-source printers available and can help you setting up your printer to successfully produce parts with TIGITAL® 3D-Set. Please get into contact with us to receive specific processing guidelines for your machine.
Typically, our materials show a re-use rate of approximately 70% or 70 to 30% with new powder. That means after sieving and recycling the powder you can use 70% again without any pre-processing. This is a very economical way to recycle our powders.
During the laser sintering process, the powder is partially melted and stabilized so that the parts reach their final shape. Remember with thermosets you need an additional curing step to reach the final properties regarding mechanical and thermal strength as well as dimensional stability.
The uncured part is called “green part” which is stable but has a certain fragility and should be handled carefully. If you consider semi-automatic depowdering the stability of the “green parts” must be taken into account.
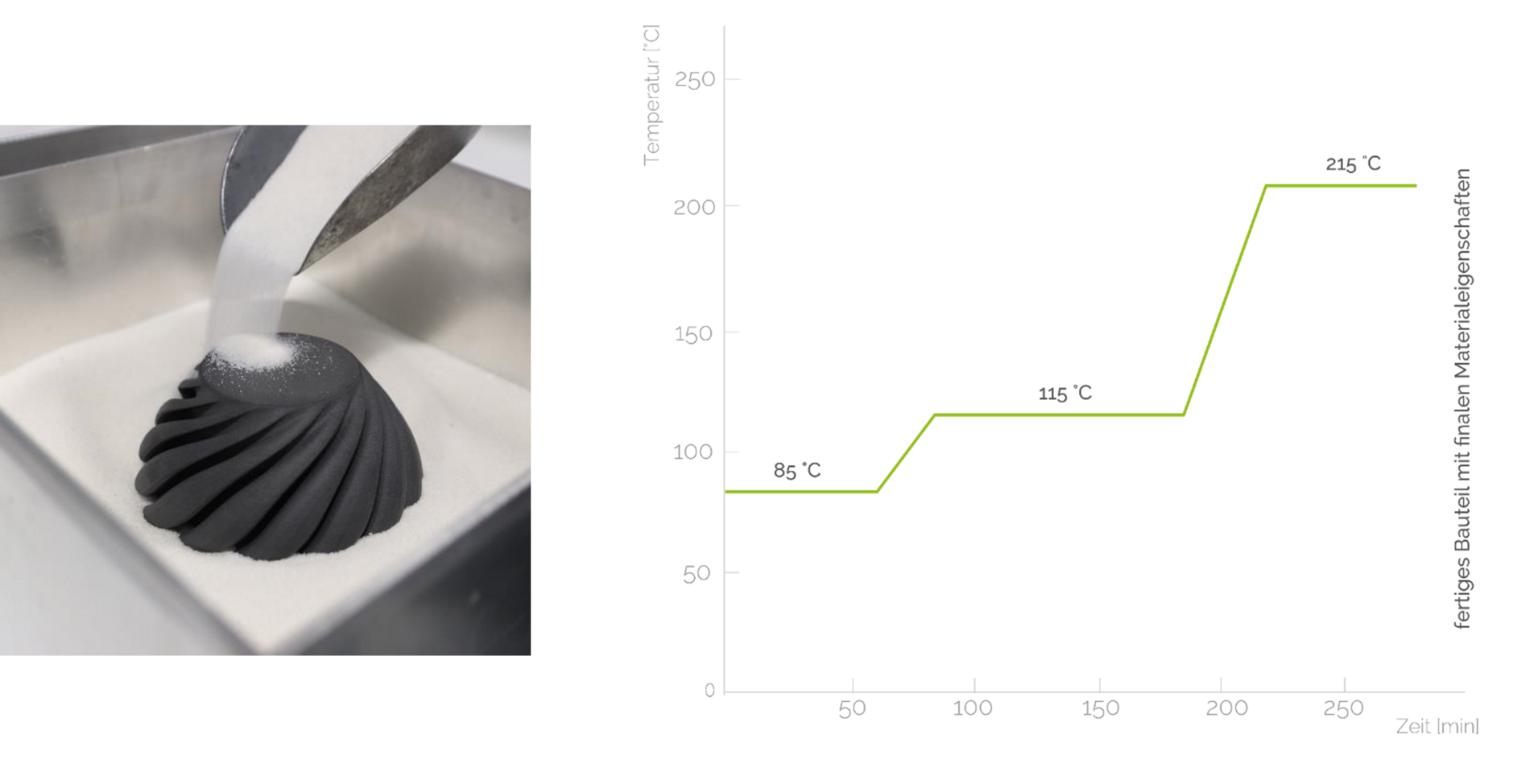
Basically, the curing conditions are depending on the part geometry and the size of the parts. If the parts have a certain complexity in shape, we recommend bringing the parts into a so called “salt bed” which stabilizes the part during the curing process to reach the dimensional stability needed.
The salt is a crystalline salt and can easily applied without any specific handling procedures. It can also easily be removed from the part with rinsing water and is not harmful for the environment.
We are helping our clients by not only qualify our materials on open source SLS printers but also in an early-stage design process where they can follow specific rules for SLS 3D printing especially with our thermoset materials. Please download our free design guide.
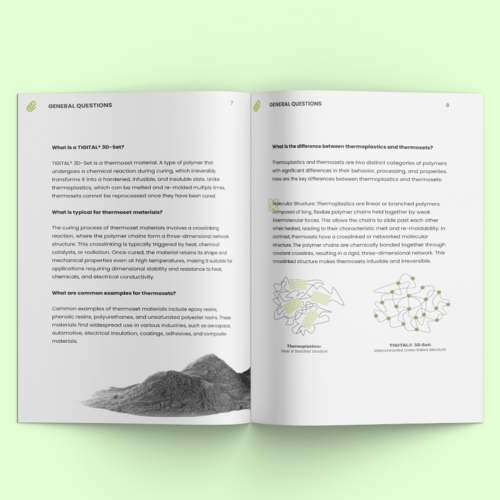
TIGITAL 3D-Set FAQ
Experience the ultimate convenience with our downloadable PDF FAQ on 3D-Set Printing materials!
With just a click, you can have all the information you need about our innovative products at your fingertips.
Download now and start exploring!